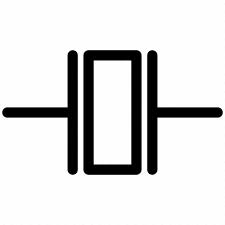
Precision crystal oscillators require a lot of testing. In fact, the testing of these devices often takes longer and is more costly than the manufacturing of the oscillator itself. That’s because the parametric requirements are very difficult and 100% yields are not possible. Further, it is only by full testing that parametric compliance and part reliability can be verified and guaranteed. There are several steps that must be carried out to complete assure this is true.
Step 1: Leak Testing
First, after the oscillators are sealed in a hermetic environment, the parts must be leak tested. The hermetic environment is absolutely necessary, because any leaks would expose the crystal to atmospheric contaminates and ruin them. The most common leak test uses a helium mass spectrometer. The oscillators are bombed with helium at high pressure ensuring that any leak would allow helium to enter the enclosure. After bombing, the parts are then measured with the helium mass spectrometer that can detect even minute amounts of helium that might leak from the package, thus detecting any very fine leaks. But before the fine leak test the parts are first tested for gross leaks by looking for bubbles escaping from the part in a liquid bath. This is necessary because if the part has a gross leak, all the helium might leak out before the fine leak test So a gross leaker might actually pass the fine leak test. For precision oscillators, both the gross and fine leak tests must be done on 100% of the oscillators. Any kind of leaker would change frequency unacceptably over time.
Step 2: Bench Tests
Next would be a series of electrical “bench tests” conducted at room temperature. Of course, the most important test is frequency as the part must be verified to be within the specified tolerance at room temperature, which could be ±1 PPM, ±10 PPM or some other value. Also at room temperature, the oscillator is measured for output power level, input current, duty cycle and rise and fall time. For many parts, the phase noise and/or jitter must also be measured using expensive and sophisticated specialized test equipment.
Step 3: Temperature Testing
Testing over temperature is next. At the very least, this will include testing of frequency over temperature. While commercial grade oscillators may get by with only testing at two or three temperatures, precision oscillators require testing at many temperatures to ensure that there are no activity dips or anomalies at any temperature. The temperature range can vary widely, but for most military or space grade oscillators the minimum temperature range will be -55C to +125C. In addition to frequency, for some parts it will be necessary to test some or all of the other bench test parameters over temperature.
Step 4: Burn-In at High Temperature
Next, high temperature burn-in of typically 7 days at 125C is performed. This is to eliminate any infant mortality of electronic components and also to make sure the frequency and other parameters do not change unduly. After this burn-in the oscillators must be 100% bench tested again and then tested over temperature again.
Step 5: Ageing
Following the burn-in, 100% of the parts are subjected to “aging”, which is a 70C, 30-day test with close monitoring of the frequency. This test is carefully defined by MIL-PRF-55310, the master USA military specification covering crystal oscillators. The frequency change data from this aging test is entered into a logarithmic formula in MIL-PRF-55310 that can predict how much the oscillator frequency change will be over more extended periods of time. Any parts that change frequency (age) too much will be rejected.
Step 6: Sample Tests
All of the tests described so far are required to be performed on all parts in the lot. But when a lot is being qualified, it is also necessary to perform sample testing that may be destructive but will further verify the parts will survive and perform as necessary in all prescribed environmental conditions and for the lifetime of the program. The most important of these tests is the Life Test. Life Test requires the parts to be put into temperature chambers at 125C for 40 days. If the parts pass the Life Test and are still meeting the parametric requirements, then they will be verified to last for years in the field.
Step 7: Special Tests for Space Parts
For space parts, there are often other tests required. For instance, very precise ovenized crystal oscillators, that guarantee frequency stabilty in parts per billion, instead of parts per million, must be temperature tested in a thermal vacuum chamber. That’s because frequency can actually change by parts per billion when tested in vacuum compared to when tested at atmospheric pressure.
Next time: Radiation Testing
Perhaps the most important special, complex and custom testing of oscillators for space involves radiation. We’ll cover that topic in our post next time.